October is National Energy Awareness Month; a national effort to underscore how central energy is to our national prosperity, security and environmental well-being. During this month, we reflect on our commitment to cutting energy waste, reducing costs, optimizing performance and advancing America's progress toward energy independence, resilience, and security.
With that in mind, American Highway is taking the opportunity to highlight three of our recent Capex projects that will reduce our company’s carbon footprint, provide a better work environment for our employees and deliver a solid return on investment for our stakeholders. These projects include:
LED lighting and motion sensor upgrades:Our Kankakee, IL, facility was using outdated metal halide lighting and T12fluorescent fixtures throughout much of the facility. These lighting options are not only a safety concern but require more maintenance, are more costly to replace due to obsolescence and consume more electricity than their LED counterparts.
By the numbers:
T12 fluorescent
-By upgrading to LED lighting and adding motion sensors, we expect to reduce our energy consumption by over 325,000 kWh annually.
-The entire job took two weeks to complete with a cost of just under $74,000 (including rebates).
-Our expected energy and maintenance savings should equate to around $50,000 per year.
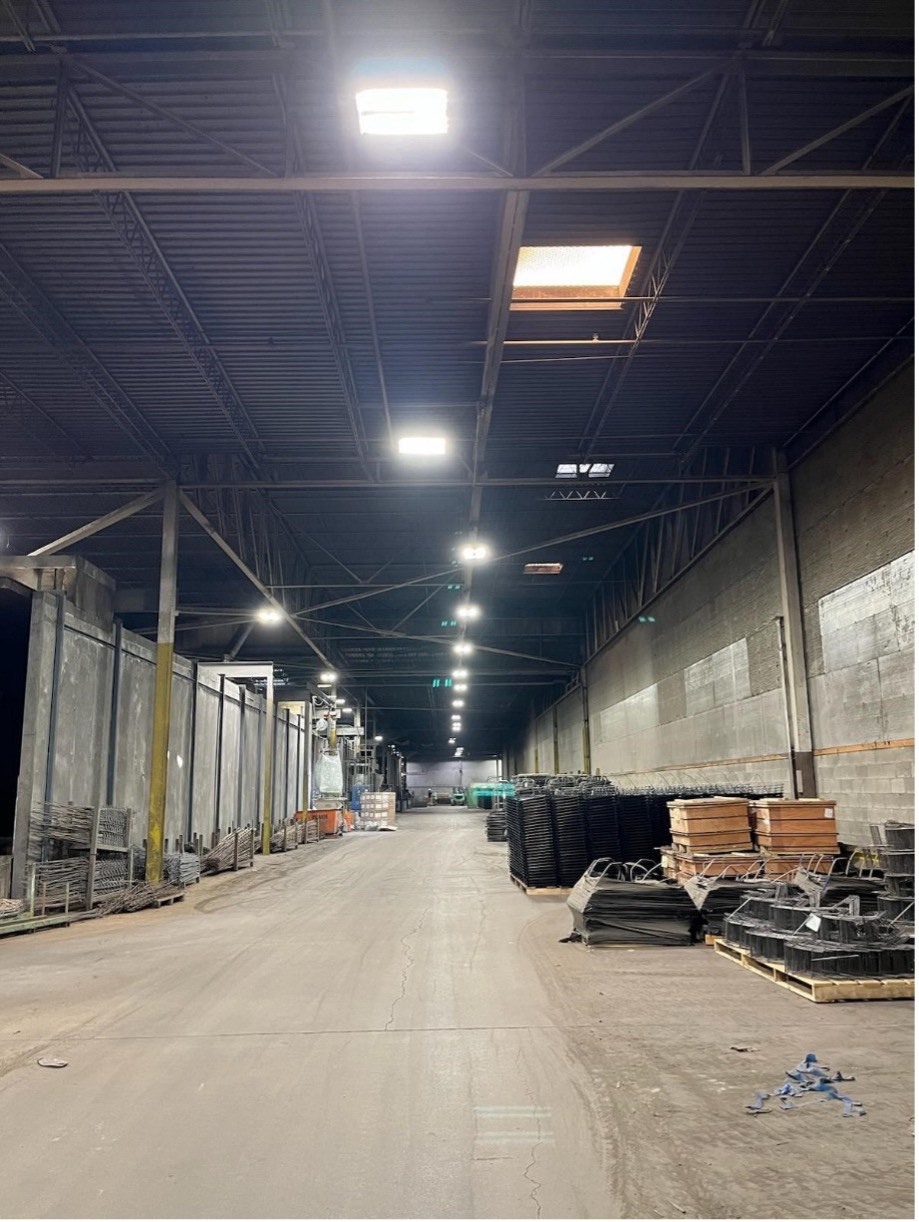
AirCompressor Upgrade (Fixed to VSD): Our Kankakee, IL, facility utilized several fixed-speed air compressors to meet our compressed air needs every day. Even with multiple units, due to their age, we still had issues with meeting our needs during peak usage periods and had to occasionally rent a unit for about $ 4,000 per week (including fuel). While VSD (variable speed drive) compressors cost more upfront, the investment provides a return through energy savings and reliability. American Highway partnered with US Air to secure a 200HP VSDcompressor that will allow us to replace our primary and secondary fixed-speed air compressors and provide all the compressed air for the plant.
By the numbers:
-By upgrading to a VSD air compressor, we expect to reduce our energy consumption by more than 125,000 kWh annually.
-The cost of the unit was just under $30,000 (including rebates).
-Our expected energy, maintenance and rental savings should equal around $30,000 per year.
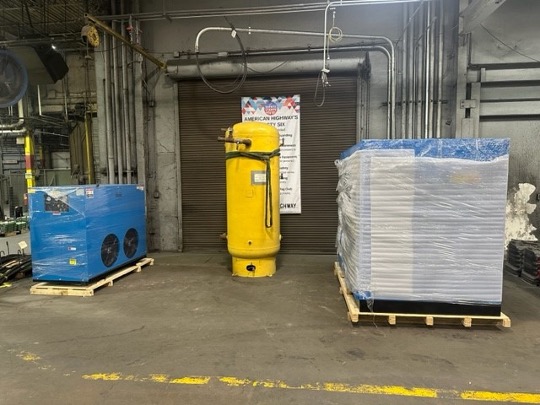
Install GasFlow Meters – Side Frame Machines: Every year, air leaks account for as much as 30% of a typical air compressor’s output. Even with a more energy-efficient VSD air compressor, air leaks result in the compressor working harder and longer—leading to additional energy consumption and cost. However, in a typical factory environment, leaks are hard to detect and are often overlooked or missed entirely. Knowing this, Ken Bowen (American Highway’s maintenance manager) identified a solution that included installing gas flow meters to Kankakee’s airlines in our side-framed apartment. The meters are already paying off by monitoring the amount of air flowing through the lines in real-time. By setting upper and lower control limits, Ken can monitor the airlines remotely and be notified of drops or increases in airflow.
Recently, the acylinder started to fail, causing a 300% increase in air consumption, which was picked up by the flow meter and relayed to Ken’s office. Ken responded to the machine in question and was able to identify the failing cylinder even though the muffler system on the machine, which actively reduces decibels to the benefit of the operator, made it nearly impossible to identify audibly.
These are just a few examples of American Highway’s continued investment in IIOT (Industrial Internet of Things) technology to enable real-time monitoring, improve our ability to accurately identify and resolve issues throughout our operations, and reduce our carbon footprint.
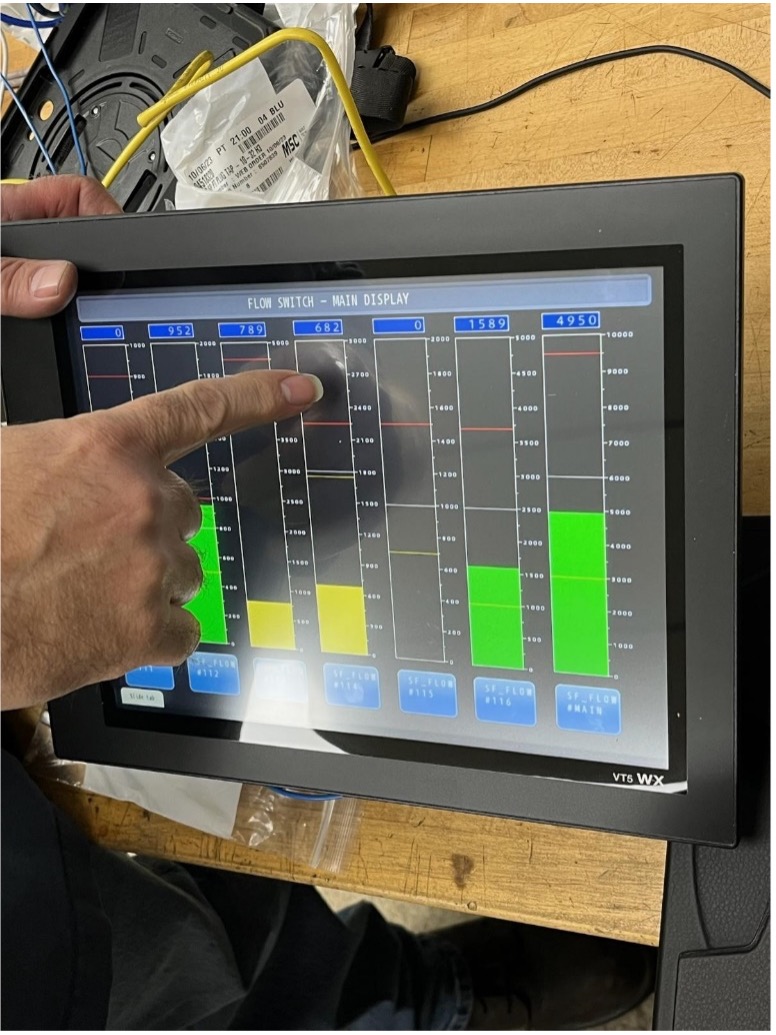
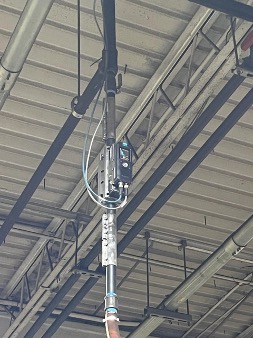